Line bending is used to make straight, precise folds in plastic components. Items like mobile phone stands are made using this process.
Before we get started here's what you'll need:
A sheet of plastic, usually acrylic is best
Access to a hotwire heater or strip heater
And a right angle or adjustable jig.
Cut the plastic sheet to the size and shape you need for your design. If you are using a CAD/CAM method then use a laser cutter. But you can also use a jig saw or coping saw and sand and finish the edges.
There are a few different options for heating plastic to bending point.
For this example, we are using a hot wire heater, but the process is the same for a strip heater.
Set the hot wire heater to the correct temperature for the type and thickness of your plastic. Acrylic like this softens at 160 degrees Celsius, but high impact polystyrene would soften at 80 to 90 degrees.
Heat the plastic until it bends easily in your fingers.
If the plastic is over 6mm thick, it will require a cooler wire and a longer heating time and will need be turned during heating to ensure that it doesn't burn.
Using an appropriate angle or adjustable jig, hold the plastic at your desired angle until its cool.
Our 3mm thick sheet will need to be held in position for two minutes, but thicker plastics would need to be held for longer.
In general, you'll need about two minutes for every three millimetres of thickness.
Once it's cooled, then you're ready to finish your plastic product.
Check out the 'Explain This… Finishing plastic' in this series for more detail.
Video summary
This needs to be done in a safe environment and always supervised.
This short film explains the process of line bending, which is a technique used to make precise folds in plastic components.
The process is demonstrated using a strip heater and a hot wire line bender. Acrylic is used in this demonstration but the process can be used for a variety of thermoplastics and across a wide range of RMT, engineering and graphic projects.
Teacher Notes
Points for discussion
- Discuss the polymer structure of thermoplastics and the heat/soften, cool/harden repeating cycle.
- Discuss the differences between thermoplastics and thermosetting plastics in terms of use and recycling.
- Discuss the types of commercial products made using similar processes.
- How you might scale up for much larger or thicker pieces of plastic?
- What are the limitations of the process? For example, only being able to bend/form in one plane.
- What are the processes you might use to create curved or compound shapes?
- When should you apply finishing techniques – before or after bending? Why?
Suggested activities
The process is used in lots of products and components:
- Mobile phone stands/holders
- Clock base in conjunction with a vacuum-formed clock housing
- Stands for point-of-sale displays
- Desk tidies/pen and pencil holders
- A cookery book stand
- A handle for a box or similar product
- Prototype model furniture
- For KS4 students, a huge range of components for product design, graphic or engineering solutions.
Suitable for teaching design and technology (D&T) at KS3/KS4 in England, Wales and Northern Ireland, and 3rd/4th levels in Scotland.
Vacuum forming. video
This short film explains the process of vacuum forming, which is an easy way to make hollow plastic mouldings which can be used in a wide variety of RMT design projects.
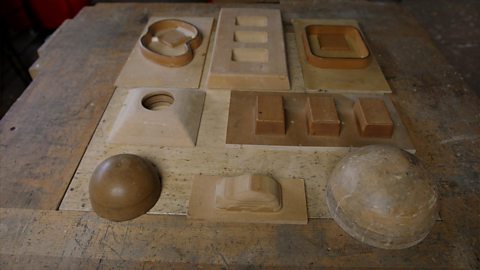
Drape forming. video
This short film explains the process of drape forming, which is used to create curved or more complex shapes out of plastic.
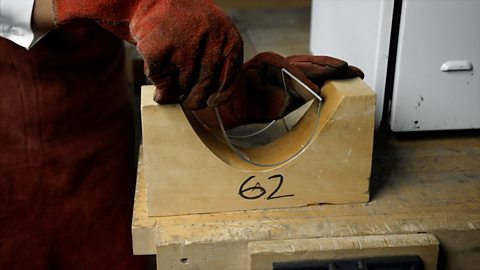
Marking shapes on metal. video
This short film explains how to mark out a design on metal before you begin cutting.
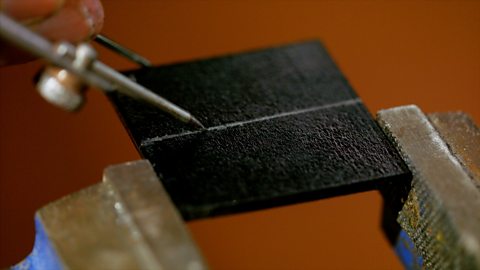